品质管理流程有哪些(品管部作业管理程序)
1.本程序文件在于规范品管部作业流程,使品管部各岗位工作有依可循、从IQC、IPQC、QA、OQC、等均有阐述具体的作业目标及作业方式、及对应时间的处理方式;各位有从事品质管理管理工作的朋友、可查看交流!
2.范围
适用于笔电扬声器行业的品管部日常品质管理工作.
3.职责
3.1 IQC进料品质管制:负责材料供应商来料的检验,来料不合格的处理.
3.2 IPQC制程品质管制:负责制程过程中对发现,反馈,跟踪问题,对员工的操作进行监督等.
3.3 QA成品品质管制:负责公司所有最终成品入库前的功能\尺寸\外观\标识进行测试和检查.
3.4 OQC出货品质管制:负责公司所有成品出货前的功能\尺寸\外观\标识进行抽样测试和检查.
4.定义
4.1 IQC原材料进料检验工作分配:
4.2 IQC原材料进料检验按照(MIL-STD-1916抽样计划Ⅲ)取样,总数≤100PCS全检:
4.3 IQC原材料检验要求参照样品\图纸和原材料SIP对材料尺寸、外观、特性、模拟实配进行检验:
4.4 IQC原材料检验按照《进料检验流程图》要求执行作业,材料品质异常按照《进料检验异常流程处理》;GP不良按照《HFS异常流程处理》。特性验证实物保存1年,进料检验报告保存3年,GP检测报告保存10年。
4.5 原材料异常急料特采范围要求:尺寸不良<5%,外观不良<8%,功能特性不良<2%为有条件特采。
4.5.1生产急料由PMC申请特采,IQC跑特采单,经过工程、生产、品管三部门主管评估确认签字,最终由副总裁决。
4.5.2原材料特采处理方式分为:增加人力随线挑选、或是线外重工两种。
4.6 IQC原材料进料检验要求事项:
4.6.1 所有正式试产和量产的原材料来料由仓管送检,并提供《进货单》给IQC检验员确认签字;
4.6.2 IQC在接到送检材料时需在4H内完成检验,并对ERP系统进行审核完毕;
4.6.3 所有的原材料厂商出货报告由IQC检验员收集整理,报告保存期限为一年;
4.6.4 所有原材料进料检验异常由IQC检验员开出《品质异常对策报告单》给SQE确认,按照《进料检验异常处理流程》处理;制程材料异常由IPQC开出《品质异常对策报告单》给SQE确认,按照《进料检验异常处理流程》处理。
4.6.5 制程反馈原材料异常由对应材料检验员5分钟内到现场确认不良实物及相关信息;确认结果及调查信息反馈给SQE复核,在2H内给出临时处理对策,72H内厂商回复完整8D报告。
4.6.6 IQC\IPQC开出的原材料《品质异常对策报告单》由IQC检验员对来料改善品进行三个生产批次数据追踪,将追踪数据报告呈送给SQE审核,无同此不良方可结案;若连续两个月未生产的机种材料,《品质异常对策报告单》视为正常结案。
4.6.7所有的原材料被投诉异常以后,供应商改善品均需在最小包装袋上注明“XX不良改善品”,便于进料检验及制程追踪。
4.6.8 所有原材料进料检验按照厂商、材料类别进行录入电子档,建立《原材料进料检验履历表》。
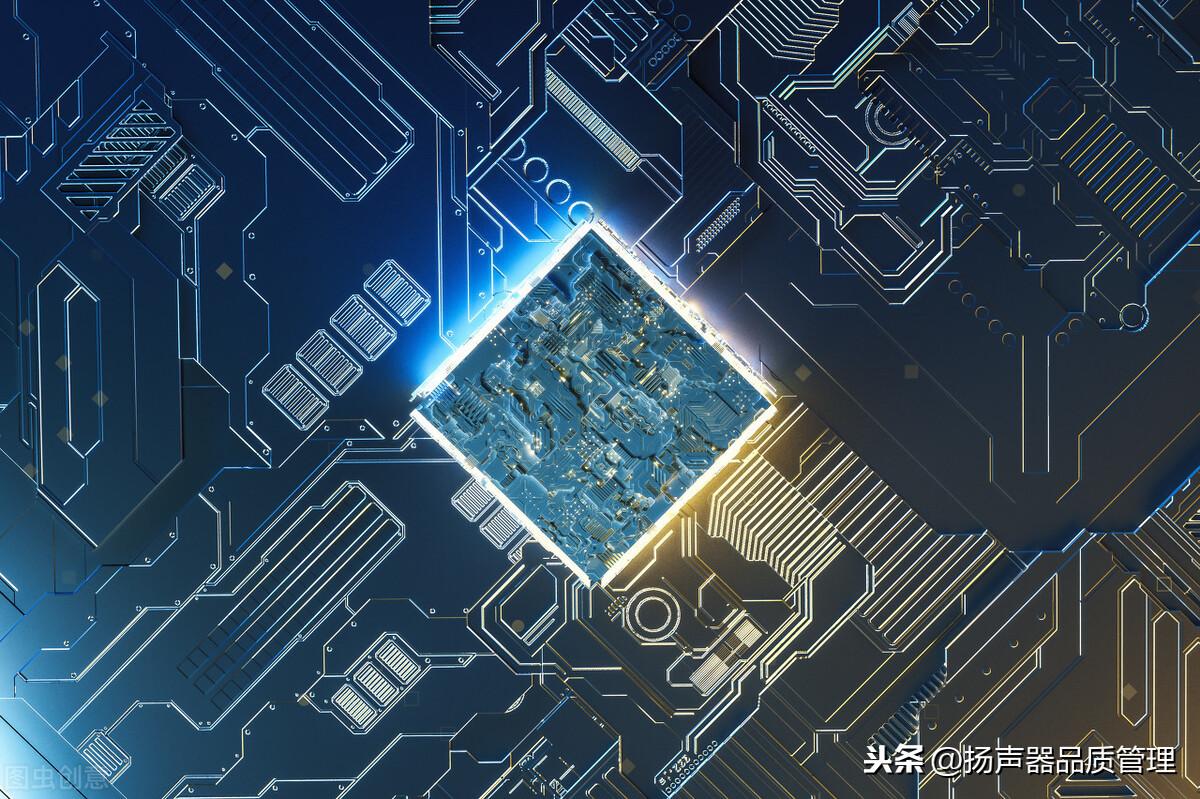
5.0 IPQC制程品质管制工作分配:
5.1IPQC工作职责要求
5.2 IPQC制程品质管制要求事项:
5.2.1 每天开线或换线时需要制作首件,需在30分钟内完成首件制作,参照《首件制作规范》作业;
5.2.2 重点岗位品质数据2H/次确认统计在《自动化过程重点数据统计表》、《一次线、超声波过程重点数据统计表》
《成品组过程重点数据统计表》中;制程单项不良超过5%需开出停线通知单给到生产主管确认处理;
5.2.3 上站IPQC接到下制程IPQC\QA投诉品质异常信息后需在5分钟内到现场确认不良实物,30分钟内给出临时对策,A类不良1PCS需开出《品质异常对策报告单》,B类不良达2%需开出《品质异常对策报告单》,C类不良达5%需开出《品质异常对策报告单》给责任单位主管、组长、IPQC确认,由PQE分析根本原因,责任单位在2个工作日内回复《品质异常对策报告单》,由开立报告组别IPQC连续追踪三批数据无同此不良方可结案,连续一个月未生产的机种视为自动结案。
5.2.4 制程A类不良定义:无音、短路、小音、音圈脱圈-开胶、U铁脱落、烧机;
制程B类不良定义:杂音、漏气、曲线不良、THD不良、极性不良、阻抗不良、漏工序、线长线短;
制程C类不良定义:变形、粘胶、溢胶、压伤、引线残线、残缺、辅料贴歪、条码模糊、PIN反;
5.2.5 原材料上线漏失A类不良达1PCS由IPQC开出《品质异常对策报告单》,B类不良达2%开出《品质异常对策报告单》通知IQC现场确认,由PQE分析根部原因,SQE反馈供应商改善并回复完整的《8D报告》;
5.2.6 原材料A类不良定义:阻抗不良、导通不良、音圈散圈、膜片开胶、尺寸不良(影响机构组装和特性);
原材料B类不良定义:变形、多料、缺料、毛边、氧化、切割不良、粘胶、分层、卷边、压痕、标记模糊;
5.2.7 原材料未达到开单要求,不良实物生产收集,由IPQC对接IQC确认不良现象,并统计在原材料《异常履历反馈表》中,每个月由SQE与材料厂商确认更换不良实物。
5.2.8 生产过程重点岗位品质管制工站IPQC 2H/次:参照《自动化组品质管制记录卡》、《一次线超声波组品质管制记录表》、《成品包装组重点岗位品质管制记录表》执行监管作业。
单体自动化:中心胶&固定点胶、引线覆盖胶、框体胶、U铁胶、引线保护胶、焊接引线、引线焊点检查、听音、测曲线;
一次线、超声波:打框体胶、焊接电子线、检查锡点、测极性、打固定点胶、压超声波、测阻抗、打线孔胶;
成品包装:量线、听音、测曲线(FO)、贴辅料、贴条码、包装;
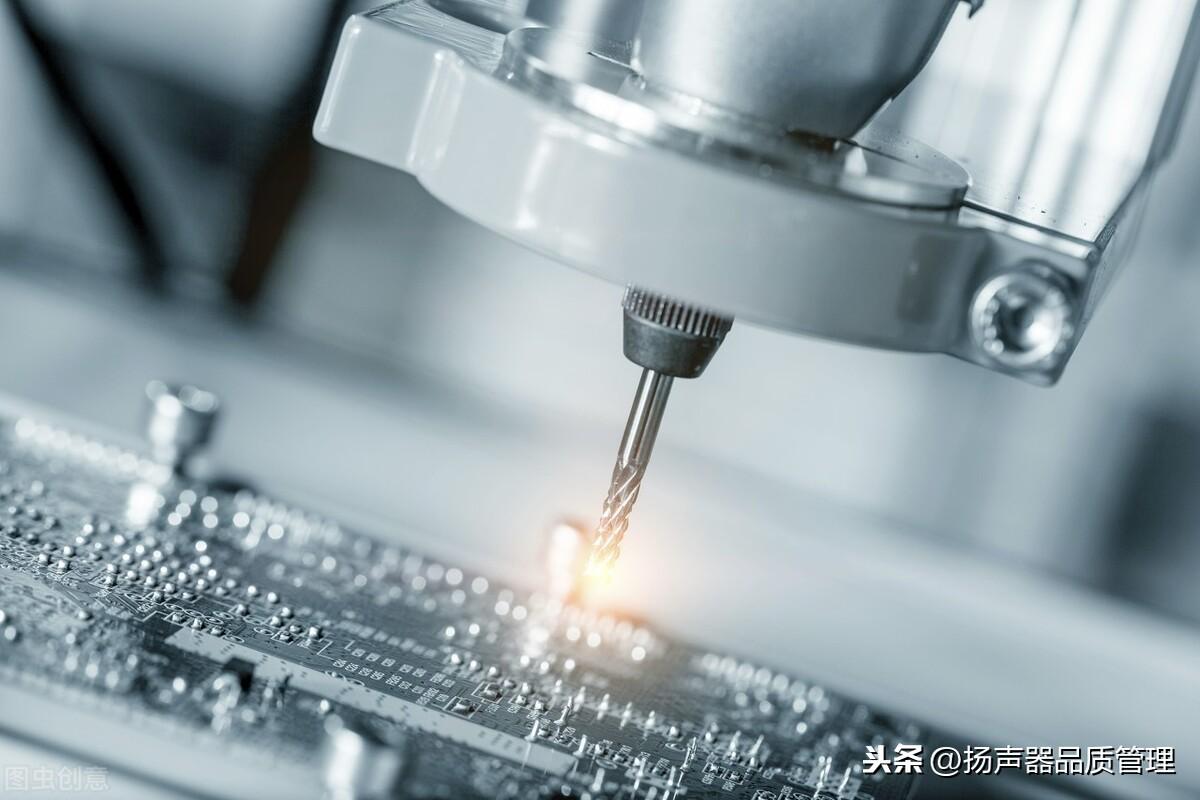
5.2.9 生产过程重点检测&检查岗位由IPQC 2H/次以投放不良品实物的方式进行监督考核,并将考核结果记录在《自动化组品质管制记录卡》、《一次线超声波组品质管制记录表》、《成品包装组重点岗位品质管制记录表》中;若考核NG需知会生产组长和主管,对该岗位人员重新培训再次考核,如果连续考核3次NG则调离该岗位,不再胜任此岗位工作;
单体自动化考核的岗位:检查引线焊点工站、听音工站、测曲线工站;
一次线、超声波考核岗位:检锡点工站、测极性工站、测阻抗工站;
成品包装线考核岗位:量线工站、听音工站、测曲线工站、检外观工站;
5.2.10 生产过程检测&检查工站不良品确认与数据统计IPQC 2H/次,数据记录在《自动化过程重点数据统计表》、《一次线、超声波过程重点数据统计表》、《成品组过程重点数据统计表》;
单体自动化不良数据统计的岗位:检查引线焊点工站、听音工站、测曲线工站;
一次线、超声波不良数据统计岗位:检锡点工站、测极性工站、测阻抗工站;
成品包装线不良数据统计的岗位:量线工站、听音工站、测曲线工站、检外观工站;
5.2.11 生产过程不良品由IPQC 2H/次跟进产线处理进度,不良品处理方式定义:
5.2.12 生产过程SOP由随线IPQC进行保管,换机种时提前10分钟将SOP发放到对应岗位作业员手中,并监督检查对应工站SOP挂放整齐且人手一份。作业过程中,IPQC需核对员工操作手法与SOP定义是否一致,并指导纠正员工按照SOP规范操作。
5.2.13 生产过程品质管制按照《制程管制流程图》执行作业。
6.0 QA成品品质管制工作分配:
6.1 QA日常工作职责要求:
6.2 QA成品品质管制要求事项:
6.2.1 QA每天开线或换线时需要制作首件,需在30分钟内完成首件制作,参照《首件制作规范》作业;
6.2.2 QA 2H/次对成品量线、听音、测曲线、检外观工站使用不良品的投放方式进行随线考核,结果记录在《成品包装组重点岗位品质管制记录表》中;
6.2.3 成品以每箱产品为一个批次,产线装完吸塑盘以后,确认数量为整箱由打包员将产品送到QA房;QA参照《承认书》、《SIP》和样品对成品功能、尺寸、外观进行检验,检验结果记录在《QA成品检验记录表》中;
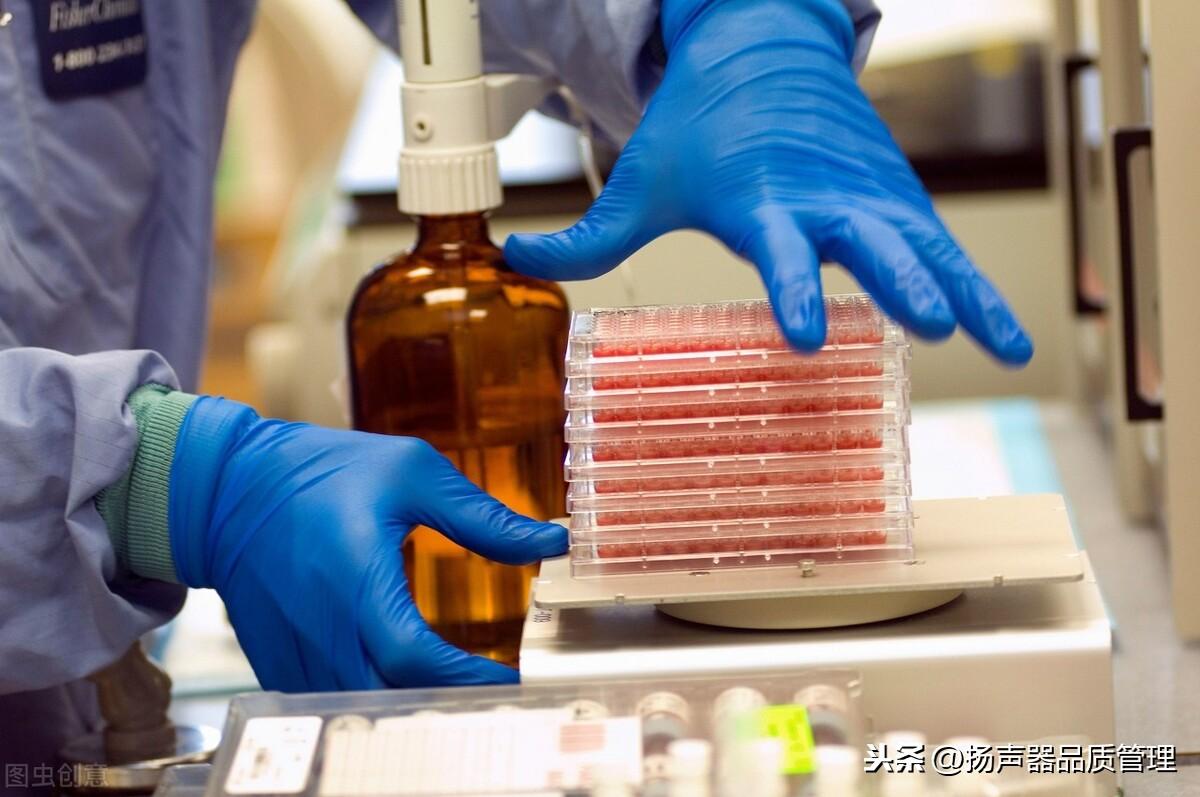
6.2.4 QA对成品检验的具体项目和判退标准:
6.2.5 QA对每箱产品检验合格以后在盖板正面上盖“QA PASS章”,并签上检验员名字,将检验结果记录在《QA成品检验记录表》中,如果当检验不良超过判退标准时需第一时间通知生产组长到现场确认不良实物,并批退当批产品重新流线检验,由QA跟进重工过程,并将检验结果和重工结果记录在《QA成品检验记录表》中;
6.2.6 QA当检验到致命缺陷无音、短路、小音、磁路脱落、音圈烧机不良时需隔离当天生产品,并开出《品质异常对策报告单》,由QA组长确认实物并组织生产主管、组长、IPQC、PQE进行分析改善,并呈报品管经理对成品做评估方案处理;
6.2.7 QA每天开线和换线前从QA房条码柜里领取对应机种使用的条码,并在《条码领用记录表》中签字;然后转交生产现场使用,中途 2H/次对产线使用的条码取1PCS样品进行扫描存档,实物粘贴在《成品重点岗位品质管制记录卡》中,扫描电子档存放在对应机种条码履历表中,每天下班以后,当天产线没有使用完的条码由QA回收存放在QA房条码柜里,并登记《条码领用记录表》回收数量及条码D/C信息。条码日期不可超过5天,尾数日期不过超过2个日期,超出标准申请报废处理。
6.2.8 QA对当天的成品检验完毕以后,按照箱号序号加贴“QA个人信息卡”(内容:箱号、标签D/C、检验日期、检验员);入库前确认外箱料号、净重、毛重、包装及环保标志(RoHS、GP、HF、UL)等信息,并在纸箱侧唛加盖“QA PASS”章。
6.2.9 《QA成品检验记录表》由QA组长审核,交到品管文员存档并将数据录入到对应机种履历表中,生成品质日报数据;当天检验数据以QA合格率计算,未达到目标值由品管文员发出《每日品质不良或超标改善报告》给生产责任主管回复改善对策;
6.2.10 QA接到OQC检验判退投诉时,需在5分钟内到现场确认不良实物,并在30分钟内给出临时对策。接到外部客户投诉时,由QA组长收集相关客诉信息及厂内库存信息,并召集QA团队开会宣导临时管控方案及厂内库存处理方案;并将客诉信息以通讯的形式反馈到生产现场管理团队及重点岗位人员知悉;
6.2.11 所有试产机种QA对功能、尺寸、外观进行全检,并将检验结果记录《成品全检报告》中;成品实物需静放12H以后再重新验证功能,最终由QA组长抽检合格以后方可入库,并将试产结果记录在对应机种履历表中。
7.0 OQC出货品质管制工作分配:
7.1工作内容:
7.1.1 按照仓库出货单对待出货成品进行品质抽检,按照(MIL-STD-1916抽样计划Ⅲ)取样,试产品和样品100%全检;
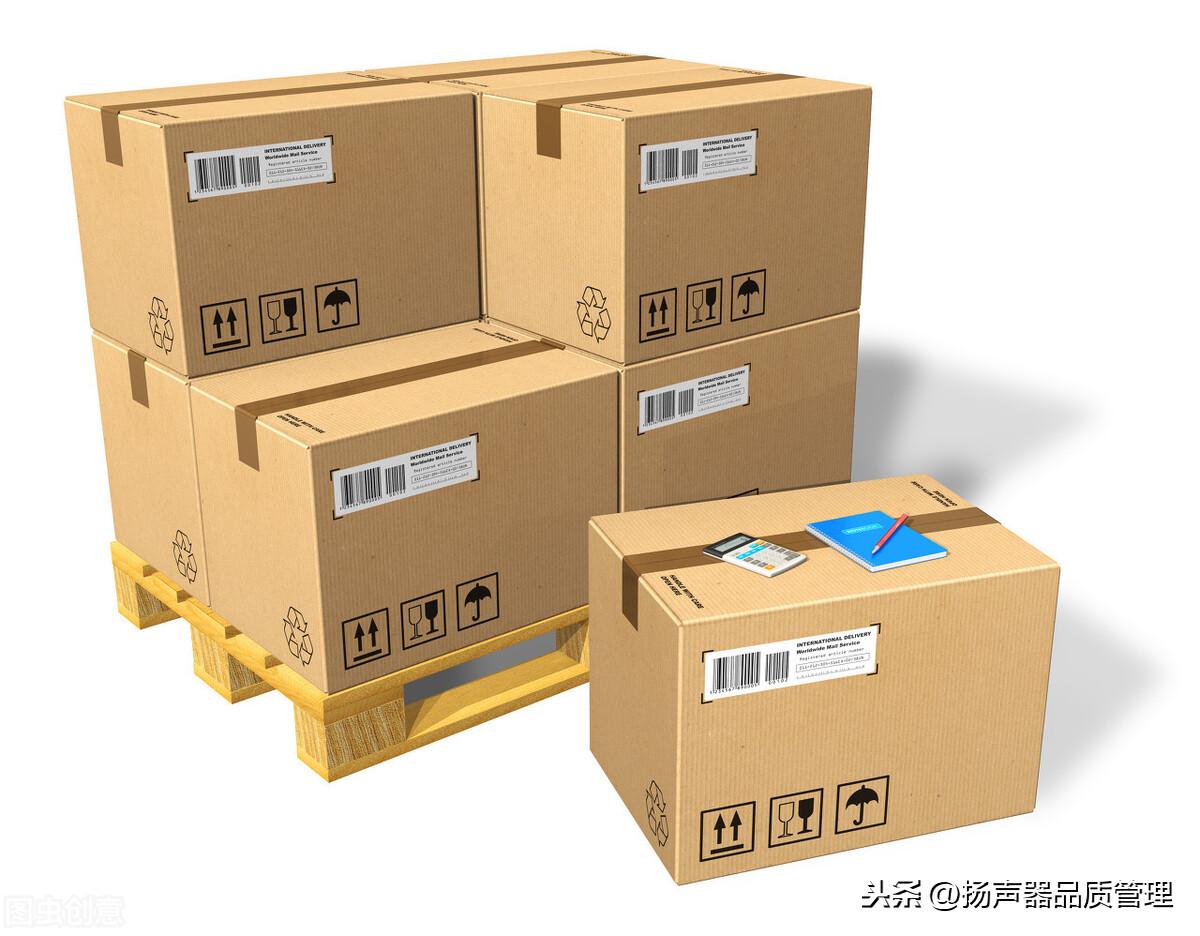
7.1.2 成品检验项目及判退定义:
7.1.3 所有成品出货产品参照《承认书》、<样品>、《SIP》对比检验,所有检验结果记录在《成品出货检验报告》中,并提报主管和品管理确认审核;
7.1.4 OQC检验产品不合格判退时,通知对应组别QA 在5分钟内到现场确认不良实物,30分内给出临时处理对策;
7.1.5 出货前需对产品外箱标签、GP环保标志、UL标签、外箱料号、净重、毛重、纸箱完好度进行目视检查,无异常则在外箱出货标签上加盖“OQC PASS”骑缝章;
7.1.6 所有出货品录入电子档履历,记录机种、组别、生产D/C、出货D/C、出货数量、检验员、箱号数,便于追踪客户端品质;
7.1.7 试产品和样品出货前需100%检查功能、尺寸、外观,并提供5套产品给DQE做ORT测试;
7.1.8 每天负责条码打印前首件确认,并将扫描结果记录在《条码首件记录履历表》中,异常《原材料异常流程》处理;
7.1.9 负责客退品确认与处理跟进,按照《客退品处理流程》执行作业;
7.1.10负责主导机种二次验证品质、主要检验对象:(小单量机型-<一万组/月;客户投诉机型、厂内制程异常机型、仓库成品呆滞料->六个月);所有以上列表物料需进行100%二次全检、不采用退货生产重工流程;但OQC当检验到CR类不良:无音.小音.短路.大杂音.大漏气.短装、漏件;外观单项不良>3%时、需开出《品质异常对策报告单》并通知对应课别负责的QA及生产负责人、到现场确认实物;并组织生产主管、组长、IPQC、PQE进行分析原因、责任单位改善,由OQC追踪结案处理、并将报告存档、便于后续品质追溯;
8.0.适用表单
《进货单》《品质异常对策报告单》 《特采申请单》 《试产报告》 《进料检验报告》《重检追踪单》 《IQC周报表》 《QA检验报告》 《首件检验记录表》《OQC出货检验报告》《IPQC巡线报表》《成品抽检合格率报表》《产品标识卡》《来料品质异常改善通知书》《GP送样指导书》《质量和可靠度测试计划》 。
本文来自网友投稿,如有侵权请发邮件给job969#foxmail.com删除,注明:https://www.969job.com/dongguan/7071.html